São inúmeros os fatores que influenciam a competitividade na indústria metalúrgica. Eles abrangem desde a geração de energia do país até a concorrência externa. Dentre os vários fatores, podemos citar que a falta de mão-de-obra, escassez de energia e a falta de inovação e tecnologia são os aspectos considerados como os maiores desafios da indústria metalúrgica em 2012.
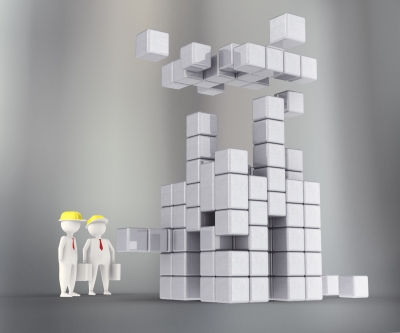
A falta de mão de obra é o principal desafios da Indústria Metalúrgica :: Imagem de Suat Eman :: Fonte :: freedigitalphotos
Falta de mão de obra na indústria metalúrgica.
A grande preocupação dos investidores é falta de mão de obra qualificada, principalmente de Engenheiros e Técnicos de nível médio em mecânica e metalúrgica.
Somente em janeiro de 2012, a indústria metalúrgica abriu 4612 vagas segundo o Caged (Cadastro Geral de Empregados e Desempregados) sendo que entre 2003 e 2008, o Brasil formou apenas 939 engenheiros metalúrgicos. ** Utilizando as palavras de Horacídio Leal Barbosa Filho, diretor executivo da ABM, em entrevista dada a revista Você S.A, se imaginarmos que são cinco anos para formar um engenheiro e mais outros cinco para fazê-lo dar retorno à empresa, é preciso agir logo”.
Ainda segundo Horacídio, “Se já está faltando engenheiro metalúrgico no mercado agora, imagine quando a produção dobrar de tamanho como o setor planeja?”.
Analisando o cenário apresentado pelos números acima, é possível ter um dimensionamento do tamanho do desafio da indústria metalúrgica neste quesito.
Consumo de energia na indústria metalúrgica deve aumentar em 40% até 2017.
A geração de energia também é um assunto que preocupa. Com o crescimento acelerado do país, a falta de energia é a maior barreira para o crescimento industrial. De acordo com um estudo sobre energia e meio ambiente do Instituto de Pesquisa Econômica Aplicada (IPEA), setores como ferro gusa e aço devem aumentar seu consumo em 40% até 2017.
O relatório defende que a solução para a indústria (que consome 35% da energia gerada no país) é investir em programas de eficiência energética e também na compra de equipamentos novos e eficientes, no que pode gerar economia de até 43%, segundo estudo em parceria com a Eletrobrás e a Confederação Nacional das Indústrias (CNI).
Um exemplo do investimento nestes tipos de soluções é o que foi implantado em 2009 pela indústria Santa Clara juntamente com a Cemig. O projeto de eficiência energética teve como escopo a modernização do sistema de ar comprimido de forma a proporcionar a redução de custos e o aumento da competitividade. Com essa ação de eficiência energética foi possível reduzir um total de 312,6 MWh de energia por ano.
Inovação e tecnologia.
A indústria metalúrgica trabalha sob a estratégia de liderança total em custos e é justamente na tecnologia que a indústria metalúrgica pode criar competitividade com a concorrência nacional e internacional.
Inovar e desenvolver tecnologias, sejam elas para redução de custos ou melhoria dos processos, devem ser abordados constantemente nos processos de melhoria contínua da empresa.
Para manter o custo competitivo é importante que a indústria metalúrgica esteja sempre bem informada com o que se passa no processo produtivo. É importante saber exatamente qual o custo do produto produzido, quanto de energia foi agregado no preço final e o quanto de material foi requisitado.
É importante analisar qual foi à participação da manutenção, quais foram os refugos e se o desempenho dos operadores está de acordo com o planejado.
Por incrível que pareça, a maioria das empresas, incluindo as metalúrgicas possuem grande dificuldade em ter estas informações precisas oriundas do chão-de-fábrica. É muito comum observar o operador no chão-de-fábrica fazer o apontamento das informações produtivas manualmente.
Muitas vezes informações estas que são geradas automaticamente pelos equipamentos e sistemas supervisórios podendo facilmente ser integradas com os sistemas de gestão ou ERPs. Com um sistema integrado, as informações são muito mais confiáveis (pois não dependem do fator humano) e não há a necessidade de pessoas especificamente para este tipo de trabalho.
Sabemos que mais importante do que gerar informações confiáveis é saber analisá-las de forma com que elas possam gerar ações eficientes. A utilização de softwares inteligentes capazes de realizar análises sofisticadas e filtrar as informações para tomada de decisões pode ser também um grande fator de competividade. Veja o artigo sobre Business Intelligence.
Não podemos deixar de falar dos softwares inteligentes de supervisão e controle desenvolvidos para a indústria metalúrgica, como as soluções que a Citisystems oferece (Perfsys e Curvsys). São softwares para máquinas perfiladeiras e máquinas curvadoras de tubos que são capazes de reduzir significativamente os desperdícios de material e o tempo de geração de receituários, com importação do projeto das peças (arquivos .dxf e .stp). Ainda possuem integração total das informações permitindo a gestão completa do equipamento no que tange a produção, eficiência global e desempenho.
Está gostando desse artigo?
Cadastre-se hoje e receba atualizações por e-mail. Respeitamos a sua privacidade e você nunca terá seu e-mail divulgado.
Todas as soluções mencionadas são maneiras eficazes de redução de custo e ganho e eficiência operacional. É preciso analisar o que é importante para o negócio e a partir disto traçar estratégias eficientes que tragam resultados perenes.
Em muitas empresas, quando se fala em redução de custos, tudo converge para redução de mão-de-obra, mas saber utilizar os recursos de forma adequada, conseguindo o máximo de desempenho é primordial e deve sempre vir antes da redução de pessoas. Só assim as indústrias conseguirão se diferenciar no mercado e manter a sobrevivência.
Fonte: Revista Veja | Revista Você SA | Exame