As empresas que trabalham com concorrência acirrada estão constantemente estudando alternativas de produzir mais rápido e com maior qualidade em relação aos seus concorrentes.
Uma ferramenta muito aplicada no chão-de-fábrica que foca a melhoria contínua dos processos é o apontamento da produção. Ele é utilizado visando o rastreamento e o mapeamento tanto do produto na linha quanto de falhas e desperdícios que ocorrem no processo fabril.
O apontamento da produção pode ser realizado de forma manual ou automática e é o grande responsável por desencadear uma série de eventos com um objetivo comum: facilitar as tomadas de decisões de forma a reduzir os desperdícios no “chão-de-fábrica”.
O propósito deste artigo é apresentar de forma clara como o apontamento da produção contribui para a melhoria da performance e as formas de apontamento da produção mais utilizadas no mercado.
Apontamento da produção
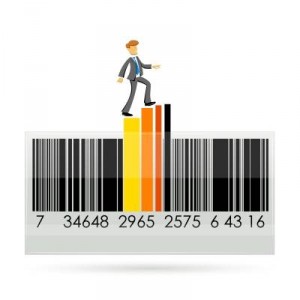
Apontamento da Produção – Sua empresa utiliza do apontamento da produção para melhorar a performance? :: Image: digitalart / Fonte: FreeDigitalPhotos
Há diversas formas de coletar as informações diretamente do chão de fábrica e utilizá-las em benefício do negócio. Pela facilidade, a mais utilizada ao longo dos anos e em muitas indústrias de pequeno e médio porte é o apontamento da produção de forma manual. Há ainda grandes indústrias que utilizam este tipo de apontamento.
Ele possui a facilidade de não exigir níveis de automação sofisticados e pode ser implementado sem a necessidade de grandes investimentos em informática e automação industrial.
Por ser realizado de forma manual, este tipo de apontamento da produção é altamente dependente dos operadores e do nível de conhecimento da equipe que atua no chão-de-fábrica.
Sendo assim, mesmo padronizada, uma ocorrência pode ser interpretada de diferentes formas dependendo de quem está inserindo as informações.
Como exemplo, uma máquina produtiva pode ficar inoperante por ter recebido o material errado para produção, mas o operador aponta que houve falta de material ou simplesmente deixa de apontar. Pegando outro exemplo da manutenção, uma máquina pode ficar inoperante por falha de um sensor de presença (falha elétrica), enquanto o operador entende que foi uma falha da cremalheira e reconhecer esta falha como um defeito mecânico.
Pelos motivos citados acima e da maior necessidade de se obter confiabilidade nos apontamentos, as indústrias começaram a empregar instrumentos de automação como câmeras, balanças automáticas e sensores para coletar informações do chão de fábrica.
A geração destas informações e o envio delas para a equipe de PCP (planejamento e controle de produção) proporcionou maior assertividade não somente no planejamento como no calculo da eficiência da produção. Assim, ficou mais fácil propor metas para a eficiência global (OEE).
Parece muito simples em um primeiro momento, mas muitas empresas deixam de aplicar estes conceitos. As razões são diversas, partindo desde a falta de cultura até o problema com recursos humanos e falta de investimentos.
Benefício da coleta de dados no chão de fábrica.
Rastreabilidade
A rastreabilidade é importante para a empresa identificar o que ocorre na linha de produção. Para uma unidade fabril que compra o mesmo produto por diferentes fornecedores, muitas vezes é impossível conferir a qualidade de todos os produtos no ato do recebimento da mercadoria.
Assim, quando o problema é percebido no produto final fica difícil identificar a origem do mesmo. Com a rastreabilidade é possível acompanhar a origem da matéria-prima com defeito e possibilita a cobrança dos fornecedores pelos danos e prejuízos ou por fornecer produtos melhores.
Obviamente, para a rastreabilidade ser colocada em prática, é preciso identificar as peças com código de barras ou mesmo, número de lote. Há muito tempo vem sendo utilizado à tecnologia de RFID por algumas companhias e esta tecnologia é chamada como “o novo código de barras”.
Controle de Perdas
Com o controle sistêmico da produção, é possível levantar o quanto de matéria-prima ou mesmo do produto acabado foram perdidos, quanto tempo os equipamentos ficaram indisponíveis para a produção e quais foram os motivos que fizeram com que os equipamentos ficassem parados.
Consegue-se identificar também se as máquinas trabalharam como projetadas para trabalhar, produzindo a quantidade que deveria na qualidade especificada. Todas estas informações são de primeira necessidade para calcular a eficiência da planta.
Está gostando desse artigo?
Cadastre-se hoje e receba atualizações por e-mail. Respeitamos a sua privacidade e você nunca terá seu e-mail divulgado.
Software para controle de apontamento da produção
Uma maneira eficiente de coletar, tratar e interpretar as informações coletadas no chão de fábrica é através da utilização de softwares específicos. Geralmente, estes softwares economizam tempo no tratamento de dados, disponibilizado as informações de forma amigável e evitando que sua equipe passe horas trabalhando com planilhas.
Todo o discurso que gira em torno do tempo e trabalho de coleta e tratamento de dados do apontamento da produção cai por terra com a utilização dos softwares específicos para o controle de produção.
Integração Com Sistemas Automatizados
Você já parou para analisar que muitas das informações necessárias para alimentar os sistemas de apontamentos podem estar sendo geradas bem antes de estes sistemas terem sido implementados?
Se você observar as máquinas no ambiente fabril, verá que a maioria dos equipamentos automatizados já faz a contagem de peças produzidas e já possuem lógicas implementadas para calcular o tempo de cada produto, a velocidade de trabalho, a temperatura, alarmes de falhas e tantas outras variáveis importantes de processo.
O motivo destas informações não serem aproveitadas no passado, reside no fato de que diferentes máquinas e equipamentos utilizam protocolos e tecnologias específicas que dificultam a comunicação entre sistemas.
Independentemente do problema inerente das diferentes tecnologias, é possível atualmente com a utilização de drivers e equipamentos específicos, não só estabelecer uma comunicação com alguns softwares existentes como aproveitar componentes e sistemas instalados que já geram informações importantes para alimentar sistemas específicos de apontamentos visando uma integração comum da base de dados a um custo acessível.
Devido ao motivo de existir uma gama enorme de tecnologias, é perfeitamente possível nos dias de hoje proporcionar controle e geração de informações confiáveis oriundas do “chão-de-fábrica” a custos acessíveis.
Com o passar dos anos, tivemos uma enorme redução de custos de componentes de automação e mais acessibilidade a equipamentos de informática. Estes recursos combinados formam uma poderosa ferramenta para controle que não pode mais ser ignorada pelas empresas, pois é através do controle que é possível entrar no ciclo de melhoria contínua e evoluir para assim ganhar competitividade no mercado.