Em tudo, desde a embalagem de alimentos até na linha de montagem de produtos, o ar comprimido é utilizado para a preparação de itens que são vendidos nas prateleiras de supermercados e lojas de departamentos. Do tanque do compressor à ponta de cada ferramenta pneumática, o ar deve ser comprimido apenas na pressão certa e aplicado aos seus alvos sem umidade e impurezas. No entanto, existem inúmeros fatores internos e externos que podem atrapalhar esse processo, o que torna crucial conhecer os 14 R da eficiência do ar comprimido.
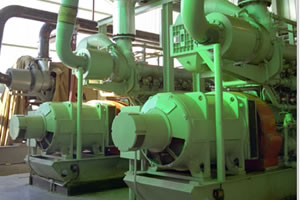
Compressores de ar comprimido
1º – Reduzir a perda por pequenos vazamentos de ar comprimido
A eficiência energética do ar comprimido é significativamente comprometida por vazamentos, que é responsável anualmente por uma perda de 20-30% no ar comprimido total na maioria das plantas. Nos casos em que não é realizada manutenção e o problema não é detectado, a perda pode exceder 50%.
Em apenas um mês, um vazamento de aproximadamente 6mm poderia resultar em uma perda de 900000 metros cúbicos de ar em um sistema pressurizado a 7 Bar. Quanto maior a pressão, mais caro e maior a perda no sistema.
Um vazamento pode ser atribuído a um dos dois fatores: um vazamento intencional, como uma válvula aberta ou drenagem de condensado; ou um vazamento involuntário, que pode ocorrer quando tubulações, válvulas, conexões de tubos ou acoplamentos são danificados ou mesmo desgastados ao longo do tempo. A vazamento também pode ocorrer se os equipamentos ociosos forem deixados em anexo a um sistema quando outras operações estão em andamento.
Os vazamentos devem ser resolvidos após a descoberta, embora exija manutenção contínua para evitar vazamentos de vazamentos. Aconselho as empresas que possuem muita pneumática a criar uma especie de equipe “caça vazamentos”.
2º – Reduzir a pressão em pontos de baixa utilização
Quando uma planta possui múltiplas ferramentas anexadas durante uma determinada operação, o sistema é projetado para produzir um nível de pressão ideal para o aplicativo de maior pressão, independentemente de o aplicativo estar ou não em uso. Conseqüentemente, a pressão externa é enviada através das aplicações de baixa pressão, e o sistema consome mais energia no geral. Cada 0,5 Bar de excesso de pressão requer 1% mais de potência.
A fim de reduzir o consumo de pressão de ar em sistemas de uso múltiplo, é melhor especificar requisitos de pressão mais baixa em equipamentos novos e reequipar equipamentos antigos para uma menor pressão. Em alguns casos, os equipamentos mais antigos precisaram ter componentes substituídos apenas para operar em níveis de pressão reduzida. Os equipamentos mais antigos que não podem ser adaptados devem ser segregados para um sistema diferente. Isso permitirá operações de baixa pressão para conservar a pressão e a energia do ar.
3º – Reduzir a pressão da fonte
Você não consegue realmente alcançar a eficiência energética do ar comprimido sem reduções significativas na pressão de descarga. Por cada queda de 0,2 bar na pressão do sistema, há uma redução de 1% nas necessidades de energia de um sistema de 7 bar. Em certos sistemas, no entanto, as poupanças são perdidas devido a tubagens mal montadas, o que pode causar operações de baixa pressão para usar quantidades maiores de energia do que o normal.
Por razões de conservação de energia, a pressão de controle de um sistema deve ser ajustada para o nível mais baixo necessário para as operações em questão – não o mais alto.
4º – Reduzir as flutuações de pressão com receptores de ar comprimido compatíveis
Nos sistemas onde os receptores são incompatíveis e a tubagem é desigual, a energia é muitas vezes perdida devido a flutuações de pressão e problemas de ciclagem do compressor. Um receptor de ar, por exemplo, pode eliminar a umidade quando se encontra na frente de um secador, mas o próprio secador pode sobrecarregar-se se o compressor de ar colocar muito fluxo de ar.
Em uma instalação que tratava o processamento de minerais, controles defeituosos do compressor resultaram em um mau desempenho. Para acomodar a sua base de 350 cv e compressores de garagem de 150 cv, a instalação aumentou o armazenamento do sistema de 400 a 4.000 L. Apesar da melhoria no controle do compressor, as questões surgiram com uma bagagem uma vez que a pressão foi reduzida. Isso se deve ao alto fluxo de ar que foi enviado através de linhas de distribuição finas. Um tanque de armazenamento foi introduzido na instalação, que liberou mais ar através de cada pulso e permitiu que a linha funcionasse a 4bar . Isso, por sua vez, permitiu reduzir a pressão sobre o sistema principal.
5º – Reduzir o número de Compressores de carga parcial
Em uma instalação de fabricação aeroespacial, três compressores de 42000 L/min foram usados para lidar com as cargas 24 horas por dia, no intervalo de 9900-21200 L/min. Devido ao alto fluxo quando a autoclave foi utilizada, 85000 L/min de ar comprimido tiveram que ser curados por até 15 minutos. Embora o preenchimento tenha durado apenas uma pequena porção de cada turno, foram necessários dois compressores devido a falhas recorrentes sempre que um estava desligado. Além disso, devido a avarias de carga/descarga, os operadores foram forçados a executar as unidades em modo de modulação de atraso.
Em última análise, este sistema foi trocado por uma configuração composta por quatro compressores de parafuso rotativo. Equipado com um controlador mestre, o novo sistema combinava as máquinas com cada carga, resultando em uma economia anual de 2.380.000 kWh.
6º – Remover aplicações de baixa pressão
Uma saída de 1 hp de uma ferramenta pneumática é o resultado final de 7-8 hp de ar comprimido. Isso se traduz em um nível de eficiência de cerca de 15%, o que, em última análise, poderá ser ainda menor se houver vazão
Quando a baixa pressão é utilizada a partir de uma fonte de alta pressão, a energia utilizada pelo compressor de ar é desperdiçada no processo. Portanto, o uso de ar comprimido para aplicações desnecessárias é uma prática cara. Como tal, quando uma ferramenta só precisa de até 1,5 Bar de um compressor de ar, é realmente mais eficiente usar um ventilador. Por exemplo, quando um armário elétrico precisa ser derrubado em temperatura, é mais eficiente usar um ventilador. Outras alternativas para ferramentas de compressão de alta pressão incluem pistolas de sopro e bombas de vácuo.
7º – Reduzir a queda de pressão
Diferenças extremas na pressão entre dois pontos em uma rede de distribuição podem ocorrer quando as mangueiras estão mal montadas nas conexões em um compressor de ar. Idealmente, essa diferença – a queda de pressão – nunca deve ultrapassar 10% da pressão de descarga que passa de um compressor de ar para qualquer ferramenta conectada. As porcentagens de queda de pressão podem ser diminuídas com o uso de válvulas de porta e passagens em forma de loop.
A queda de pressão geralmente ocorre com compressores de ar mais antigos – muitas vezes, os que não são realmente adequados para o uso atual, mas, no entanto, foram adaptados a uma variedade de ferramentas em expansão. Conseqüentemente, esses compressores geralmente estão mal equipados para atender às demandas atuais. Particularmente problemático é quando o comprimento dos tubos e as taxas de fluxo são inadequadas porque a tubagem do sistema foi determinada pelo tamanho da conexão de descarga do compressor. A velocidade máxima do ar utilizada em todo o sistema de tubulação nunca deve ultrapassar 50 ft/s (fps).
8º – Remover a umidade de acordo com as necessidades da aplicação
Os requisitos do ponto de orvalho variam de um aplicativo para outro. A secagem do ar, no entanto, não deve exceder o nível necessário para uma determinada aplicação. Em alguns sistemas, um secador é colocado em linha para o compressor com a finalidade de secar tudo no mesmo nível, independentemente do uso ao qual o ar está sendo aplicado. Isso pode ser um uso caro da energia.
Para muitas aplicações básicas, uma pressão geral do ponto de orvalho de secagem de 3 °C é suficiente. No entanto, os tubos e drenos através dos quais o ar é passado devem ser levados em consideração, especialmente se houver temperaturas de congelamento ao longo do caminho. Você pode economizar energia, revisando cada aplicativo para avaliar as necessidades de secagem e ajuste o secador de acordo quando uma determinada aplicação está em andamento.
9º – Remover o condensado enquanto conserva o ar comprimido
O condensado é drenado de várias maneiras pelas máquinas que formam um sistema de compressão de ar comprimido. Dependendo do clima e dos fatores ambientais de um determinado local de trabalho, as necessidades de um sistema podem variar. Quando se trata de tamanho de drenagem, as seleções devem ser feitas com base na taxa de condensação esperada para a localização em questão, bem como a taxa de contaminação esperada dos lubrificantes aplicáveis.
Sem manutenção adequada, os drenos e as armadilhas obstruem gradualmente dentro. Isso faz com que o excesso de umidade se acumule no sistema e se forme gradualmente na água, o que pode ter os seguintes efeitos:
- Corrosão nos tubos e no receptor de ar
- Mau funcionamento das válvulas
- Erosão de lubrificantes ao longo de cilindros e válvulas
- Agotamento de filtros e secadores
Uma prática defeituosa que muitas vezes é empregada envolve deixar a válvula de drenagem ligeiramente aberta, o que faz com que o ar comprimido escape. Independentemente da armadilha de drenagem, a melhor maneira de garantir a manutenção é na forma de tubulação de derivação.
10º – Reduzir o tempo de inatividade com manutenção preventiva
Os problemas potenciais com um compressor de ar devem ser rastreados antecipadamente e corrigidos antes que eles conduzam a reparos onerosos e tempo de inatividade. Mesmo que um lubrificante possa ser garantido para durar por x número de horas, os filtros e separadores em que o lubrificante é aplicado podem falhar mais cedo, se não monitorados caírem na pressão, tomam seu pedágio.
Quando um microprocessador mostra sinais de manutenção necessária, a questão deve ser tratada imediatamente. Os drenos de condensação também devem ser inspecionados rotineiramente por sinais de angústia. Mantenha arquivos em mãos de todos os ajustes e substituições de peças. Os intervalos entre essa manutenção podem ser usados para determinar a freqüência necessária para reparos e exames.
Em um caso que veio exemplificar os problemas com supervisão de manutenção, uma fundição teve que alugar um trio de compressores a diesel para compensar seu próprio sistema de atraso. O problema decorreu da má manutenção do seu próprio sistema de quatro compressores na fábrica de roda ferroviária. Não só isso causou o atraso do sistema, mas também fez o ar muito quente e fez com que os refrigeradores tropeçassem.
Descobriu-se que os compressores de ar internos vazavam 30000 L/min por semana. Além disso, uma máquina não se abriria na entrada enquanto outra não estava carregando. Depois que o sistema sofreu uma série de reparos muito necessários, a planta economizou $ 90,000 por ano com um sistema reduzido a apenas três compressores.
11º – Registre dados sobre manutenção e reparos
Devem ser mantidos registros de todos os procedimentos de manutenção para fins de análise e configuração de prioridade. Ao rastrear a freqüência de quando a manutenção ou reparos são necessários em uma parte específica de um compressor de ar, é mais fácil configurar um cronograma em frente de quando realizar inspeções. Desta forma, também é mais fácil prever um orçamento de manutenção, porque você conhecerá a freqüência em que determinadas peças serão devidas para reparo ou substituição.
Com os registros de manutenção disponíveis, você também pode identificar quais áreas mais freqüentemente precisam de atenção e os tipos de medidas geralmente necessárias para corrigir um determinado problema. Também devem ser observadas notas de como um componente específico se comporta, tanto antes quanto depois da manutenção. Isso pode ajudá-lo a solucionar e determinar se um problema é isolado ou sistêmico.
12º – Regulamente mudanças na utilização do ar comprimido
Para acompanhar as mudanças no uso do ar, ajuda a observar níveis de pressão ao longo de pontos específicos no sistema. Uma coisa que isso não deixa claro, no entanto, é a taxa em que esses padrões de mudança ocorrem. Para isso, é aconselhável manter um registro de dados.
À medida que os anos passam, uma fábrica tipicamente apresentará novos compressores de ar e eliminará os antigos. No final de operação, deve ser dada atenção às flutuações de pressão que podem ocorrer quando um novo componente funciona a um nível de uso diferente do que uma maquinaria mais antiga adjacente. Nesses casos, atualizações adicionais podem ser necessárias, e é melhor encontrar essas coisas mais cedo e não mais tarde.
13º – Recuperar o calor
Na maioria dos compressores rotativos refrigerados a ar, 80% da potência resulta na geração de calor para o resfriador de óleo, enquanto 13% da energia restante é usada pelo pós-arrefecedor de ar. Uma quantidade substancial de calor pode ser recuperada dessas operações e pode ser redirecionada para outros fins.
Por exemplo, em uma fábrica de recondicionamento de garrafas de pequena cidade, 15kW de calor são gerados por um compressor de ar de 25 hp. Com as garrafas penduradas de um transportador para o recondicionamento, a maioria do calor é usado para fins de secagem, enquanto o calor restante é usado para limpar o ar na instalação. Isso resulta em cerca de R$ 9.200 de poupança anual de energia.
14º – Reduzir o custo de energia – Ar comprimido
Como parte de um esforço colaborativo em toda a indústria conhecido como The Compressed Air Challenge, as plantas que utilizam compressores de ar estão empregando todos os tipos de manutenção preventiva e técnicas de conservação de energia para reduzir custos operacionais, minimizar reparos e tempo de inatividade e melhorar a qualidade dos produtos acabados.
Em muitas plantas com sistemas multi-compressores, melhorias operacionais permitiram o desligamento de pelo menos uma máquina, o que levou a grandes economias de energia e manutenção. As empresas são capazes de ganhar mais dinheiro com seus produtos porque há custos reduzidos envolvidos. Com o desempenho da máquina muito melhorado e as operações sem defeito, a qualidade do produto melhorou substancialmente em muitas indústrias participantes.
Coautoria: Leonardo Sanches do Carmo
Especialista em Pneumática Industrial, formado em Tecnologia de Eletrônica Automotiva na FATEC Sorocaba (Faculdade de Tecnologia “José Crespo Gonzales”) e técnico em Eletroeletrônica pelo SENAI de Alumínio (“Antônio Ermínio de Moraes”). Atualmente Pesquisador da FAPESP (Fundação de Ampara à Pesquisa do Estado de São Paulo) na Empresa CitiSystems.